LEAN Construction
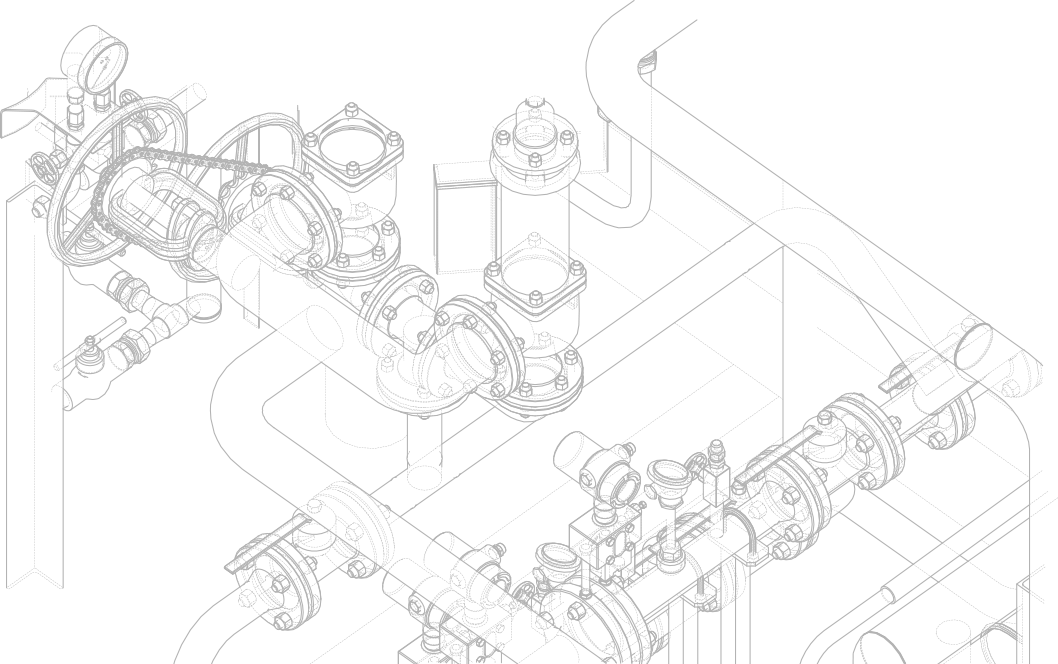
LEAN Construction Principles & Management Services
Our LEAN Construction Process
5 Why Analysis
We utilize critical problem-solving techniques to find the root cause of a condition by asking ‘why’ successively (at least five times) whenever a problem exists. As each answer is documented, we make an additional inquiry concerning that response.
Target Value Delivery
This management practice ensures the facility meets our customer’s needs and is delivered within budget, and promotes innovation to increase value and eliminate waste.
This practice also assists the customer with budgeting to determine the target cost, conditions of satisfaction, and risk/opportunity registry. Continuous estimating to update projected costs versus target cost is based on:
- New Information or Site Conditions
- Design Changes – Value Engineering
- Field Performance – Just-In-Time Deliveries
- Cost control is used to ensure on-time, on-budget delivery of the conditions of satisfaction.
Virtual Construction
With virtual construction, we use three-dimensional, real-time, dynamic building modeling software to see the geometry, spatial relationships, geographic information, quantities, and properties of building components of the project.
Virtual construction provides the platform for simultaneous conversations related to the design of the “product” and its delivery process, thereby speeding the field delivery process (or construction timeframe). We use Trimble to increase the accuracy of field layout and clash detection.
Planning & Scheduling
Each phase is planned using Pull Planning and a high-level schedule is developed early. This schedule is developed based on project milestones and initial budgets.
Murphy Company also utilizes the Last Planner Process for project production planning and control to create a workflow that achieves reliable execution. This collaborative, commitment-based planning system integrates ‘should-can-will-did’ planning.
Continuous Improvement
Lean projects ensure feedback is frequent and monitored so the team can improve its performance through:
- Plus/Delta feedback for every meeting.
- Periodic formal surveys.
- Culture of mutual respect and accountability.
Murphy is an active participant in Lean communities of practice to keep current on industry best practices in delivering Lean projects. Lessons Learned is an active component of the Murphy Way for all projects, including Lean.